Newsletter Resins & Additives for Coatings
Applied digitalization and big data:
“Exploring a mountainous island, looking for the highest point”
How you can use Design of Experiments to predict the characteristics of 100% UV coatings
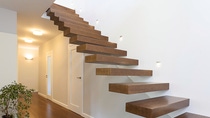
When it comes to finding the best UV formulation for your needs, is there a better way than experience and intuition? We interviewed BASF expert, Dr. Wolfgang Gaschler, to find out how the Design of Experiments method and a growing set of data can unlock new possibilities in your formulation development …
Firstly, what is the Design of Experiment method?
At BASF, we are committed to using advanced methods and digital tools to create real, measurable value for our customers. One of the most exciting ways we can do this is by using Design of Experiments (DOE) when formulating UV coatings for our customers.
DOE is a statistical model that we can apply when we are looking for a new formulation for a specific purpose. It allows us to adjust variables to look for multiple properties at the same time – viscosity, hardness and so on – while maintaining prediction accuracy. This will potentially allow us to discover an optimal formulation with far fewer experiments than it would otherwise take, thereby saving our customers time and money.
How does it differ from conventional formulation methods?
The more conventional scientific process would be to start from first principles and proceed from there, one variable and one adjustment at a time. You can arrive at excellent results this way, of course, but the number of experiments required could run into the hundreds.
The analogy I use is that formulating coatings is like exploring a mountainous island, looking for the highest point. To find the top of the mountain easily, you need a good view of the terrain. In this analogy, every experiment is like revealing a section of terrain.
You can proceed the traditional way, one step at a time: the first experiment reveals some terrain on the shoreline, clearly not near the highest point, so you make another experiment nearby but slightly closer to the center, then closer, closer again… By contrast, DOE is like making a systematic sweep of the island, getting an overview of all the peaks and viewpoints in this unknown territory. This allows you to take a direct route – choosing your experiments in a way that optimizes them to provide the maximum amount of information with the minimum number of iterations.
Is DOE a brand-new technique?
No – in fact, the principle has been around for 100 years! However, advances in computing and software have made it easier than ever to apply. I am not much of a ‘computer person’, but the software is so intuitive that I can effortlessly get the most out of it. This is the result of a continuous journey of insights and improvements, demonstrating that the concept works and gaining experience in getting the best out of it. At BASF, we make the most of this experience by passing it on to our customers, giving them good suggestions for optimum formulations and the right support to make the process really work for them.
So, if it isn’t new, how come it isn’t used by everyone?
There is still reluctance to use Design of Experiment, particularly among formulators who have more experience. This experience gives them a high degree of intuition – a ‘mental map’ of the unexplored territory. According to this ‘mental map’, some of the experiments suggested by the statistical approach do not make sense. To continue our analogy, it might look like the system wants to scan a section of terrain surrounded by water – surely nowhere near the highest point! But when you perform the experiment, it will turn out that there is some useful information there – a hidden viewpoint that helps you find the peak more quickly.
Nevertheless, this is why people may be hesitant to use the approach. However, I suspect that this will change as more and more chemists and engineers try it and discover its benefits.
Is this just for UV systems, or does it apply to other formulations?
DOE has numerous applications, but UV coatings are one of the very best. Simply put, this is because UV is a 100% system: active ingredients, and nothing else. This enables us to be highly accurate with our predictions.
Here is how it works. You start with a defined set of properties you are looking for, or a problem you need to solve. If a customer came to me and said, ‘Here is what I need to do: I want to achieve a certain viscosity, a certain hardness, and a best price,’ we would combine the desired outcomes with the database of BASF products to give us our starting set of data. We fit the data to a statistical model, and use it to make predictions that we base experiments on. The software can handle all the variables at once, enabling us to make great steps with every experiment.
At the end, the customers not only receive the formulation they need, but also the confidence that we are not missing any information that could lead us to an even better result.
So, would UV formulators really benefit from switching to the DOE method?
Personally, I’ve been using DOE for 10 years, and I wish I had started even earlier than that! Once I started, I soon discovered that it gives you much more information, and it makes the analysis of your data more straightforward, than conventional data. In short, your data starts to work a lot harder for you.
In my opinion, all our customers could benefit from it, if they are not already. It can enable them to get the most out of UV technology, which is in itself a promising field. It gives reliable results, whether for formulating something new or for finding alternatives to an existing solution. It’s not like learning a new language, where years of training is needed; we can use it to generate benefits for you almost immediately. That’s Design of Experiment: significant opportunities with very little risk.