Dispersions & Resins
“Switching to water-based technology is an opportunity to future-proof your converting business”
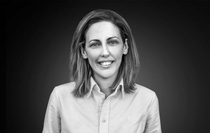
Tell us about Druckfarben’s story so far as it relates to packaging.
DRUCKFARBEN HELLAS S.A. is an industrial company catering to the ink and paints sector, specializing in flexible packaging, decorative paints and energy-saving systems.
We have two manufacturing facilities in Greece, one in Romania, and three service and distribution centers situated in Bulgaria, Serbia and Nigeria. Our products are also distributed through a network of dedicated partners in Cyprus, Malta, Albania, Kosovo, Northern Macedonia, the Gulf countries and North Africa.
Collaborating with the biggest groups in the flexible packaging industry, we pride ourselves on providing innovative, sustainable solutions for our customers’ requirements. The key to achieving this? Our people. The diverse experience, creative thinking, talent and ideas of our employees make anything possible.
Our dedicated R&D team – composed of chemists, engineers, color and application specialists – plays a key role in this. Our manufacturing team uses state-of-the-art instruments and tools to ensure the highest quality of our products.
DF’s engineers provide technical support to existing ink mixing stations, with the handling of inks, and also support printing processes and application inquiries. We regularly organize training seminars for our customers, plan recurring on-site visits and support this with off-site technical support, ensuring optimum results in every printing job.
How did your switch to water-based inks work?
We took a hybrid approach, producing and supporting both solvent and water-based technologies.
Our vision is to be an innovative, eco-responsible partner, with a customer-centric approach, always delivering the best and most responsible solution for our clients. When it comes to water-based inks, we have invested in new technologies and solutions, since we regularly receive new requests for sustainable solutions and demanding applications.
Are there any differences in performance between water and solvent-based inks?
The main differences we perceive between solvent and water-based inks are higher energy requirements during the drying process, different type of adhesives for lamination, and slower printing and laminating speeds. However, we know it is possible with the correct measures to obtain the desired results with water-based ink. We recommend to our customers that they contact their ink and OEM suppliers about the best printing machine settings for the products they wish to print.
To be clear, as an ink manufacturer that offers both solvent and water-based products, water-based products are not always recommended as the first choice for every type and structure of lamination. For example, there are still some challenges to achieve optimal performance on triplex or high-demand printing structures (e.g. for retort, sterilization, etc.). However, new water-based products offer promising results on BOPP, alum foil, PE and woven substrates.
A recent example is a client of ours who prints polyethylene bags for fertilizers. After testing water-based inks with our support, the conclusion they reached is that water-based inks meet their requirements, performing accordingly in terms of light fastness, water fastness, rub and scratch resistance, and alkali fastness. Shifting towards water-based inks will allow them to have an eco-friendly solution without compromising the quality of their packaging.
Why did you decide to join the PRETHINK INK network?
The flexible packaging sector is moving quickly towards sustainable solutions and technologies. We want to participate in the innovative actions that will accelerate this transition and bring a new generation of sustainable technology to our fields of interest. The PRETHINK INK network, comprising companies throughout the flexible packaging sector, is a creative idea that will help us to attain a better understanding of the properties of water-based inks and how to obtain optimal results with them for every application. Through networks such as this one, companies involved in the flexible packaging industry can share their ideas and findings.
Why is ink base an issue more stakeholders in the flexible packaging industry should be interested in?
Water-based inks are evolving and improving all the time. Today, more than ever before, converters can achieve higher-quality printing results. Furthermore, water-based inks in general conform to the latest legislation and food packaging regulations, are safer for the environment, and are well perceived by our customers. Switching to water-based is an opportunity for converters to differentiate themselves from competitors, to boost their environmental credentials, and to future-proof their businesses while meeting customer needs today.
Do you have any advice for companies considering switching to water-based inks?
To really get the best out of water-based inks, you need to adapt your process management. The factory configuration and manufacturing process should take into consideration the handling, storage and life cycle of the product. It is important to mention that water-based inks ensure a friendly environment for printing technicians, leaving fewer toxic residues behind (no PVC/phthalates). New developments are always taking place and further reducing VOC emissions. Last but not least, from a business perspective, water-based products in many cases offer remarkable performance at a competitive price.
What do you think the future holds for inks and packaging as a whole?
In all industrial sectors, we will see increased demand for sustainable technologies that contribute to a circular economy. Maximizing technological capability while minimizing environmental impact is the only way forward – not only with the increasing demands of the market requiring us to move to sustainable solutions, but also due to legislation requirements. Recently, raw material suppliers, ink producers and converters had to handle the reclassification of MIT as an ink can preservative, as well as restrictions on using primary aromatic amines in final and intermediate products.
Another critical subject is micro-plastics. As plastic production grows, the need to limit micro-plastic pollution becomes more urgent. We stand the best chance of achieving this if the entire value chain works together – which is necessary for the adoption of sustainable ink.
A few facts about our interview partner:
Name: Vanessa Panagiotopoulou
Role: Water-based inks lab supervisor
Company: Druckfarben Hellas
Founded in: 1970
Specialisms: Inks for flexography and rotogravure printing, including HSL, varnishes, primers, additives and specialized products serving our customers’ stringent requirements.
Describe your company in a few words: Innovation, enthusiasm, integrity, collaboration, accountability, reliability.