Dispersions & Resins
“We must investigate every potential way to advance sustainability”
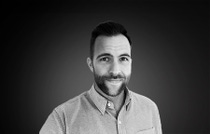
Tell us about SAUERESSIG’s story so far as it relates to packaging.
We support our customers from initial idea to final packaging. In addition to steel cores and sleeves for gravure printing as well as high-quality printing and embossing dies, we provide our customers with relevant advice and individual design-to-print management. Our tools are particularly used for flexible packaging in the tobacco and pharmaceutical industries, and we regularly create designs for fast-moving consumer goods brands.
We are always looking for new ways to add to our portfolio, with our c.INKTEC Innovation Center providing a space to generate creative ideas. Our goal is to allow customers to present their products in the most appealing manner possible, using a combination of professional services and innovative technologies.
How did your switch to water-based inks work?
In the field of flexographic printing, we have been working on water-based inks for quite some time. We launched materials specifically designed to further optimize ink transfer with water-based inks. With these properties, even the ink consumption in the printing process can be reduced. We have also begun to explore this with water-based engraving inks. This is where our c.INKTEC laboratory comes into its own, giving us the in-house capability to test our tools in combination with water-based inks to enhance quality and color consistency.
We initially carried out tests on our barrel proofer to find out which technical parameters would give us the best results in terms of color density and printing behavior. We then progressed to testing with our project partners on a commercially available rotogravure printing machine. The first results of these production tests were very good. Of course, the gravure cylinders for water-based ink need different settings to solvent-based inks. But the outlook is promising and I’m sure that, used correctly, water-based inks will show the same printing results as solvent-based.
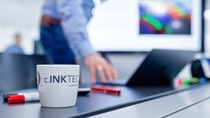
Are there any differences in performance between water and solvent-based inks?
Water-based printing inks contain water as their main component and can be diluted with a water-alcohol mixture or only with water. Therefore, they do not cause issues with solvent retention.
Another difference is the cell depth of the anilox rollers. With water-based inks, flatter cells are used, which can be emptied easily. The ability to formulate water-based inks with a relatively high pigment content means good ink coverage can be achieved even with low ink film thickness. In addition, the polar forces of water-based pigments are beneficial for dot-sharp printing.
Why did you decide to join the PRETHINK INK network?
For us, partnerships and teamwork are a central factor in driving innovation. If we can bring together companies with different points of view and combine them as a team, it will increase our success across the board. We see the printing industry coming closer and closer as more companies realize this. We are now fully organizationally aligned towards collaborating with the supply chain to reinvent traditional materials and techniques. Minimizing the use of solvents is one way to do this.
Why is ink base an issue more stakeholders in the packaging industry should be interested in?
Ink turns a blank carton into a lasting impression. It helps products and brands express their identity. When you look at packaging, its color is the first thing you notice. Therefore, from a marketing point of view, a balanced color concept and the right color control are very important. So ink choice is central to your sustainability and commercial goals.
The use of water-based inks is worthwhile for the entire supply chain: achieving a high level of performance with fewer resources.
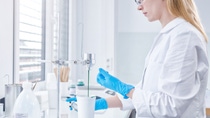
Do you have any advice for companies considering switching to water-based inks?
Be open to something new, even if we are talking about processes that have not changed for a very long time. We must investigate every way to advance sustainability, including areas that are still largely untouched. As an industry, we have to reinvent ourselves in many areas. Even if it requires work and expenditure at first, it is worth it.
What do you think the future holds for inks and packaging as a whole?
Our task is to continue to inspire consumers with packaging, while ensuring it becomes more sustainable. These two processes should not just occur independently: they need to be interlinked. When we design branding and packaging, we should already be thinking about how it will go back into the recycling loop.
A few facts about our interview partner:
Name: Christian Groh
Role: Global Manager | c.INKTEC Department
Company: SAUERESSIG Group
Founded in: 1953
Specialisms: Services for pre-press stage, rotary tools for gravure and embossing applications, flexographic printing and special machine construction
Describe your company in 10 words: Improving the printing industry sustainably with our inventive spirit and expertise.