Dispersions & Resins
“Going water-based helps improve efficiency and eliminate waste”
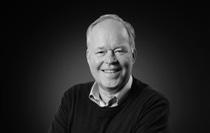
Tell us about GSE Dispensing’s story so far as it relates to packaging.
In 1985, GSE was the first company to introduce automated dispensing of water-based inks to the packaging industry. Since then, we have continuously developed innovative dispensing equipment for all packaging printing applications: narrow and wide web; labels, paperboard and flexible packaging. Our dispensers are suitable for all liquid ink sets (flexo, gravure and screen) and can be configured to accommodate water-based, solvent-based and UV-curing inks. Our modular design architecture enables rapid configuration of our solutions – even for custom installations.
In 2018 we launched the game-changing GSE Ink manager software to support ‘lean and smart’ control of ink management and printing operations. Today, we have more than 2000 automatic dispensers and software packages installed at factories in 90 countries. We are supported by a global network of sales, service and supply chain partners.
Why did you decide to join the PRETHINK INK network?
Our company mission is to reduce the environmental impact of inks and related resources. Switching to water-based inks can make a significant contribution to this. Therefore, we were keen to support this initiative.
One of our four corporate values is to be connected. We believe that by joining forces with other partners in the network, we can help eliminate waste from our mutual value chain.
What is your role in the switch to water-based inks?
With our solutions, we can help converters make a successful switch from solvent to water, at a pace that suits them. For example, our dispensers can be extended to accommodate up to 34 base ink components – enough to support a converter’s complete color needs for two ink sets. So converters can run solvent and water-based at the same time – switching one press at a time or gradually running down their stocks.
Our software for storing and easily recalling ingredients, linking with color formulation software, enables the converter to get the same color results when transferring from one set to another – so the customer sees no change in quality.
What are the differences between water and solvent-based inks?
There are some differences in how water-based and solvent-based inks need to be dispensed, handled and managed.
Water-based inks are safer for operators as they do not have the same explosion risk. This means there is no need to invest in explosion-proof dispensing systems, or grounding against electrostatic discharge. With a solvent-based system, these additional measures would be necessary to obtain 114-ATEX approval and the associated CE certificate in the European Union.
As a result, water-based inks can not only be safer and more sustainable, they can also help drive down expenditure when it comes to facilities and equipment.
Would you need stainless steel equipment like fixed tanks and pipes for water-based inks?
As a matter of fact, fixed stainless steel tanks and piping are not required for solvent or water-based inks! It’s our experience that some customers request this kind of equipment anyway. Although we are able to offer these products in stainless steel, we generally recommend using interchangeable containers and durable, flexible hoses. The benefits of these products – saving equipment costs, increasing flexibility and improving handling efficiency – apply to both ink types.
Why is ink base an issue more stakeholders in the flexible packaging industry should be interested in?
Ink itself accounts for a small percentage of a printing business’s operational costs. But there are a number of hidden associated costs, which come from managing, processing, production, shipping and – for some sectors – batch tracing inks. When you take these into account, changing the ink base can have a surprisingly large effect on costs and value.
For example, the trend to keep mono-pigmented colors separate from the technical medium gives the converter more flexibility, and can even eliminate the distribution step from the supply chain. Also, when using water-based inks, the converter does not have to comply with explosion-proofing regulations, thereby reducing equipment and handling costs.
Do you have any advice for companies considering switching to water-based inks?
It all depends on your situation – whether you currently buy pre-mixed inks, mix manually, or already operate an automatic dispenser. Our general advice, however, is to view the switch as an organizational change process and think ‘lean’. Look for ways to improve efficiency and eliminate waste. As part of this, selecting the right hardware and ink management software is paramount.
How do you see the future of inks for flexible packaging?
Consumers are becoming more and more eco-conscious, and rightly so. We have to do a better job as industry to meet their demands. We can boost our sustainability in a number of ways, such as reducing resource use, and producing packaging that is recyclable, reusable, compostable or easier to sort. And as far as inks are concerned, switching to water-based is certainly the sustainable pathway.
A few facts about our interview partner:
Name: Anne Lourens
Role: Managing Director / Co-Owner
Company: GSE Dispensing
Founded in: 1975
Specialisms: Engineering, production, commissioning and servicing of ink-dispensing systems and ink management software
Describe your company in a few words: We produce equipment, software and services for managing ink throughout the production workflow.