Dispersions & Resins
“If you want to be prepared for the future, you have to change as early as possible”
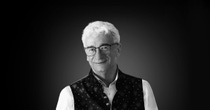
Dr. Kai Baer, Managing Director at adphos
Tell us the story of adphos so far as it relates to packaging.
adphos offers advanced Near Infrared (aNIR) technology that enables near-instantaneous drying with reduced thermal stress on the substrate.
Packaging has been important to us from the very beginning. Our first application was inkjet printing on thermal paper. Most inkjet printing for graphical applications has used water-based ink for some time, and when we started, everybody was using recycled paper, which is very porous, and ink would penetrate strongly into it. Conventional drying methods take a long time, and in some cases, you would lose printing sharpness because of the ink penetrating too far before it dried.
With our technology, immediately after the inkjet application, we were able to set the ink on the surface and dry it before it had the chance to penetrate into the substrate. At the same time, there was very little heat conduction into the substrate. These are both important factors for packaging, because it is usually fully coated, which means drying is an issue, and it is temperature-sensitive in most cases.
What was your initial involvement with water-based inks?
We have had a strong focus on water-based technology throughout our history. Inkjet is an area where we are very strong: we have more than 2,000 applications realized with our technology.
Flexible packaging is undergoing rapid change, and we strive to drive this change further and faster. For some time, on temperature-sensitive materials, almost everything was UV or solvent-based. People assumed that the only way to avoid thermal stress on temperature-sensitive materials is to use solvents or UV. But when we demonstrated that our technology is able to dry water-based inks on thermal sensitive materials, that was a big change point.
The trend today is now fully in this direction. Companies are getting more critical of systems that include solvents and photoinitiators. Market leaders are driving towards water-based and requesting that everyone else does the same.
Are there any differences in performance between water and solvent-based inks?
The biggest realization that we need to reach here is that switching to water-based is a holistic change. You should not assume that you can just replace your ink and ignore everything else.
For example, ink that is applied on contact printing technology usually only has to be physically dried, which means the liquid has to be removed. If you go for inkjet technology, however, you need to remove not just the water but also the humectants that are added to keep the nozzle opening configured correctly. We sometimes hear people say, ‘The ink does not dry properly – it smears.’ Smear resistance comes from adhesion to the surface, and if it’s not porous, the humectants will prevent this from occurring. Therefore, you need another way to achieve durability: adjusting your substrate or your post-print process.
This does not have to be difficult! But it does mean, first and foremost, thinking about ‘water-based systems’, not ‘conventional solvent-based systems with the inks changed’. This is still not fully appreciated in the market, which is why we need to talk more about it with all stakeholders.
Why did you decide to join the PRETHINK INK network?
Education and knowledge transfer are key to increasing understanding of how water-based inks work, getting the best out of them, and minimizing issues. We have learned a lot about them already. When interest initially grew in changing from analogue to digital, people initially thought that the only difference was contactless printing compared to contact printing technology. But in truth, many aspects of the behavior are different, including optimal ink selection. As an industry, we were slow to learn this at first.
That’s why a holistic approach to these systems is a must – otherwise, you are never able to provide a system that is optimized for the product and the process. This is why the PRETHINK network is very valuable. Different value chain representatives – ink, inkjet technology, integrators, substrate, post-print – sharing knowledge and competencies and engaging in active two-way communication. Through this, we can start talking and learning about applications from an early stage.
Why is water-based ink an issue more stakeholders in the flexible packaging industry should be interested in?
If you want to be prepared for the future, you have to change as early as possible. This does not mean you have to go 0-100% tomorrow. You can be structured in your approach, establishing the most urgent areas and selecting reference projects to start with. But overall, there is a clear understanding that we all need to consider water-based as much as we can.
A lot of people think there are disadvantages to water-based ink. I see it the other way round: I see significant advantages. No longer being concerned about smell, about treatment of liquid, about any leakage in the process. These are advantages. But you may need some different processes, and you may need to evaluate your substrate too. Being aware that this needs to be a holistic process re-evaluation puts you in the best position for success.
Do you have any advice for companies considering switching to water-based inks?
We still often hear stories like, ‘I made this one switch, and it didn’t work.’ The key is to realize that it is not just the ink you should be looking at: a holistic approach is needed. Take water-based ink as the start of a reconsideration of your whole process.
This doesn’t mean you have to throw everything away that you do now! But you have to take into account that there are new boundary conditions, and re-evaluate the different interfaces and outcomes to make the change work. Don’t just think you can replace your ink and everything will be the same as before. Evaluate the very process you are doing.
What do you think the future holds for flexible packaging?
I would be surprised if uptake did anything but grow. Market players, consumers and societal trends all point this way. People – not just in our industry but in society as a whole – will become more and more sensitive to different ingredients and risks. Therefore, in printing and coating, as much as we can achieve it, we will go water-based.
If I could put money on this happening, I would do so, 100%.
A few facts about our interview partner:
Name: Dr. Kai Baer
Role: Managing Director
Company: adphos Group
Founded in: 1994
Specialisms: Drying, heating and thermal processing with a focus on print, graphics and water-based technology.
Describe your company in a few words: We do not copy-paste; we adapt all our processes to optimize productivity, quality and cost.