Dispersions & Resins
“Water-based ink makes a holistic contribution to sustainability”
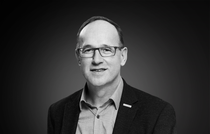
Tell us about Follmann’s story so far as it relates to packaging.
Follmann began producing inks mainly for the napkin industry. To help meet regulatory requirements, we started producing water-based printing inks not only for napkins but also for other paper-based packaging. Soon we expanded into further areas of packaging like film and foil.
Now, we are pioneers in the application of water-based printing inks on flexible packaging. We are working on a range of substrates while maintaining a high quality. Packaging manufacturers in the consumer goods industry rely on our water-based printing inks appreciate their reduced VOC emissions compared to solvent-based options.
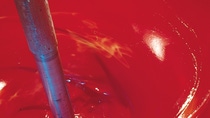
How did your switch to water-based inks work?
For many substrates, we have never formulated anything else. Since 1984 we have offered water-based systems for table decorations and wallpapers. About 10 years ago, working with a sustainability pioneer in the consumer product sector, we started making water-based inks for flexible packaging. In addition to the reduction of VOCs, which have a negative impact on occupational safety and on climate footprint, we managed to reduce wear on printing plates and achieve a saving there.
We are closely monitoring how preferences are evolving and are aware that our customers need our expertise. Making connections along the entire value chain will be even more crucial when it comes to addressing future issues. A closely aligned network will more effectively develop solutions in the interest of end customers; a single person couldn’t manage the same outcomes.
The PRETHINK INK initiative is therefore a good way of consolidating knowledge and enabling our partners and customers to enjoy success. Just exchanging a solvent-based product for a Follmann ink won’t result in optimum performance. Every factor – ink, press design and all parameters – must be coordinated. We must work together to bring together these factors and achieve maximum impact without a reduction in press running speeds.
Are there any differences in performance between water and solvent-based inks?
Printers will notice a change to elements of their workflow, such as cleanability, foaming or viscosity control. This is where we come in and support our customers in changing systems, from the laboratory to handling, production and post-processing. Using our expertise, we help customers manage this overall change, supporting them with quality and safety management through each production process.
In terms of performance, overall comparisons between water-based and solvent-based inks often miss the mark: the benchmark covers NC, PU, PVB and PVC-based portfolios, so this generalisation is not helpful. Each solvent-based product is used for a specialized performance attribute: printing speed, mechanical properties, chemical or physical characteristics. In addition, each substrate and application is different. The correct products must be chosen, and the right buttons pressed on the printing machine, to achieve the desired results.
Our overall assessment is that the distinction between the two products is marginal, if any. With the right machine parameters, coordinated hardware and correct handling, you can achieve comparable results with our printing inks: For example, our customers report the same process speeds and print qualities in reverse printing.
Substrates such as PVC, PLA, OPA or aluminium can vary in terms of printability – but this is also the case with a solvent system.
Why did you decide to join the PRETHINK INK network?
Working together on issues and challenges is hugely valuable. Widespread change in a traditional industry like printing can only be achieved by a network of partners.
For example, if a printer has a problem with foam formation, the press operator might decide that the water-based portfolio does not work. But they could avert the issue with the right information on the handling of processes, workflows, and tool set-up. We work with our value chain partners to give them this sort of crucial information. Our comprehensive service includes making the know-how we have acquired available to everyone.
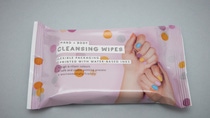
Why is ink base an issue more stakeholders in the flexible packaging industry should be interested in?
The improvement of occupational health and safety is a strong argument all on its own. The reduction of explosion risks is also a positive – and leads to more affordable evaluations by insurance service providers. In addition, there is the proven evidence of reducing CO2 emissions by replacing solvents with water and dispensing with natural gas for operating the afterburner. With increasing restrictions and penalties for VOC emissions, making the switch could be financially worthwhile in the near future.
Customers have reported an efficiency benefit of up to 30 percent with water-based ink. You also enjoy a higher level of process reliability because, for example, the quality of the printing plates is not degraded by solvents.
Our products make a holistic contribution to sustainability: climate, product safety and occupational health and above all total cost of ownership.
Do you have any advice for companies considering switching to water-based inks?
Get in touch with us and we will show you the viability of water-based ink – not just on printing machines but also throughout the whole value chain. We will work together with you to specify your individual packaging design and manage the steps of the transition: selecting a portfolio, converting machines, adapting workflows.
It is also important to involve your employees on site at an early stage. Driving everyone’s engagement is the most important building block for successful change.
A few facts about our interview partner:
Name: Roland Geiselhart
Role: Director, Business Unit Print & Packaging
Company: Follmann GmbH & Co. KG
Founded in: 1977
Specialisms: Water-based printing inks for flexo and gravure printing, high-performance adhesives and microcapsules, decorative and functional coating systems, and water-based ink receptive coatings for digital printing applications.
Describe your company in 10 words: We create tailor-made products and individual solutions for our customers.